Table of contents:

Video: High-tech renaissance mechanisms. Part 2
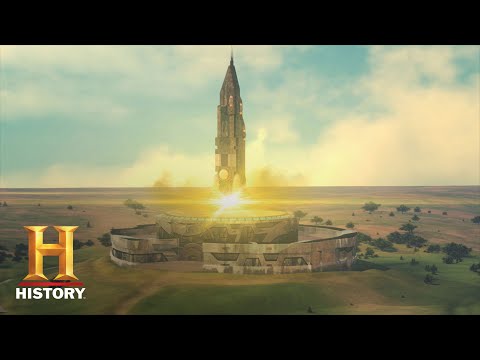
2024 Author: Seth Attwood | [email protected]. Last modified: 2023-12-16 15:55
We continue our excursion through the technologies of the highly developed culture of the Renaissance.
Peacock clock
The watch was made in 1770 in England. Intended as a gift to the Chinese emperor, but were sold to Prince Potemkin for a gift to Catherine II. The watch was delivered disassembled and some details were lost on the way. They were restored and repaired by I. Kulibin, who was already a mechanic at the Academy of Sciences.
The clock is still in working order. They are turned on once a week to maintain their working condition. Every 15 minutes, music sounds and figures of three birds come to life. The elements of the movement are made of silver and gilded copper.
On the left is a watch from Germany, circa 1550. On the right is a clock from the 16th century, the British Museum.
Even then, there was a high level of engineering. Before manufacturing, you need to calculate the gear ratio of the mechanism so that it accurately moves the arrows in accordance with the duration of the day. And for this, it was necessary to attract astronomical observations, or to be tied to the countdown of other previously made clocks.
But this is a table clock. At the end of the 16th century. there were also miniature ones, here are examples:
One can only admire the engineers of that time. Or, as they are called, simply watchmakers.
Modern assembly process for Swiss mechanical watches:
But before assembly, all these parts must be made with the highest precision! Now all calculations are done in the program and parts are made on CNC machines. How was it before?
Modern production of gears for large clocks on lathes. I think it was exactly the same before.
The gear plates still had to be cut straight.
Right - Merklein Rose machine, 1780 for creating symmetrical multi-petal parts. Left: Lathe, London, 1838
Apparently, it was on machines with this principle of operation that gears for watches were obtained. Not manually.
Machine tools 17-18 centuries
I showed other examples of machines of that time in the previous part.
We can already say with confidence that various machines were not only at the beginning of the 19th century, but also in the 18th century, and maybe even earlier. This is evidenced by such products as barrel organs, music boxes, watches, medieval robots (automaton dolls).
The level of engineering thought in them is at a high level. Unattainable for modern handicraft production. And many say that stupid ancestors used to live.
Gear manufacturing technology is an interesting question. There is no information anywhere about this process. The gears in the watch rotate in bushings. In modern - in ruby. And how were friction units made then, and in particular bushings in machine tools? Or how did you do the bearings? Or is there everything on the bushings too?
Another kind of masterpiece of engineering and musical abilities of the masters of the 18-19th centuries. - these are barrel organs and music boxes:
Now it is difficult to imagine that some master would combine his talents in something like that. Maybe those masters wrote their music for such devices?
But this automation is 18th century. more "flowers". Look at the androids of the day who could write and play musical instruments!
Official information about this robot doll says: it was made in 1770. Swiss watchmaker Pierre Jaquet-Droz. This automaton is capable of writing sentences up to 40 characters long with a quill pen: “I love you, my city” or “Pierre-Jacquet Droz is my inventor”. The author gave it the name Calligrapher. The growth of the robot doll has a five-year-old child. The structure consists of 6000 parts … The body is made of wood. The head is made of porcelain.
The doll does not just write sentences, she is still dipping a quill pen into an inkwell, shaking it off, turning her head, supposedly following this process and following her eyes. Pierre Jaquet-Droz has been making the doll for two years.
The author-designer also created clocks with singing birds and fountains. But he has two more works of engineering thought: the "Drawer" and "Musician" dolls.
The musician consists of 2,500 parts. She sat at a small but real harpsichord and played music by pressing the keys. She was able to perform five compositions. The doll even "breathed" and moved its eyes in the same way.
The doll can paint a portrait of Louis XVI and an image of his dog Tutu.
All three dolls are in the Museum of Art and History of Neuchâtel and still work.
I think these are only products of the unique engineering skills of the craftsmen of that time that have come down to us. To repeat this now, you need the work of a team: from designers to specialists in turning.
Previous part
Recommended:
Western mechanisms of world enslavement

Over the past centuries, the concept of Western colonialism has remained practically unchanged. Having become more sophisticated, its mechanisms have remained approximately the same as at their dawn. As before, countries that do not have resources, but usurped technologies, as well as control over the emission of currencies, exploit and threaten those who have subsoil and cannot give back
7 custom mechanisms that look like science fiction machines

Man is such a creature who constantly invents something to improve his life. Some of the things that talented engineers create seem incredibly strange from the outside. Moreover, the field of application of these devices is far from always immediately clear and obvious. In reality, most of these devices are incredibly useful. Let's look at a few of these
Hidden mechanisms of slavery

It would seem that each of us does not have an iron collar, but in the modern parasitic system, a person is bound hand and foot by many other, non-iron chains. Ignorance, ideology of consumerism, economic dependence and other "achievements" of civilization
Mechanisms for the transformation of mass culture. Derivation of morality

Report of the editor-in-chief of the projects Teach Good and CinemaCensor Dmitry Raevsky on the influence of mass culture and the mechanisms of its transformation. The report was presented at the Northern Business Forum "Livadia-2019", its main provisions were also announced during the conversation on the "Tomorrow" TV channel with the child psychologist, publicist Irina Medvedeva and teacher, writer Tatyana Shishova
"Do you believe in God?" Mechanisms for zombifying Jehovah's Witnesses

Thanks to a well-organized advertising campaign, only the lazy today have not heard of Jehovah's Witnesses. Free Magazine Racks