
Video: Lost construction technologies of St. Petersburg
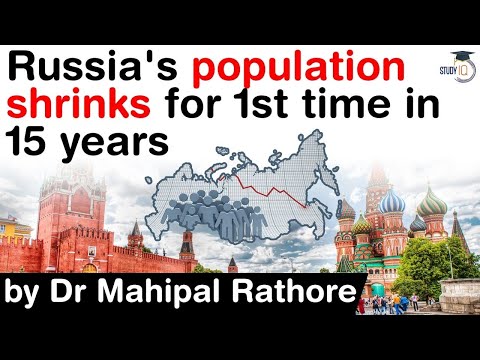
2024 Author: Seth Attwood | [email protected]. Last modified: 2023-12-16 15:55
In the middle of summer 2013, I watched a series of popular science films from the “Distortion of History” series, which were filmed based on the lectures and materials of Alexei Kungurov. Some of the films in this series were devoted to construction technologies that were used in the construction of well-known buildings and structures in St. Petersburg, such as St. Isaac's Cathedral or the Winter Palace. This topic interested me, because, on the one hand, I have been to St. Petersburg many times and love this city very much, and on the other hand, while working at the Chelyabinskgrazhdanproekt design and construction institute, it never occurred to me to look at these objects before these films precisely from the point of view of building technologies.
At the end of November 2013, fate smiled at me once again, and I was presented with a business trip to St. Petersburg for 5 days. Naturally, all the free time that we managed to carve out was spent on studying this topic. The results of my small, but nevertheless surprisingly effective research, I present in this article.
The first object from which I began my inspection, and which is mentioned in the films of Alexei Kungurov, is the General Staff building on Palace Square. At the same time, in the film, Alexey mainly mentions stone door frames, while I quickly discovered that this building has many other noteworthy elements, which, in my opinion, unambiguously reveal the technology that was used in the construction of both this object and and many others.

Rice. 1 - entrance to the General Staff building, upper part.

Rice. 2 - entrance to the General Staff building, lower part.

Rice. 3 - entrance to the General Staff building, corner of the "jamb", polished "granite".
In his films, Alexey pays attention mainly to the "pasted" rectangular fragments, which are visible, for example, in Fig. 2. But I was much more interested in the fact that the seam that separates the details of the structure does not go where it should be if these details were really carved from a solid stone - fig. 3.

The fact is that one of the most difficult elements to manufacture when cutting is the inner triangular corner, especially when cutting such a hard and brittle material like granite. At the same time, it does not matter at all whether we will cut granite with a modern mechanical tool or use, as we are assured, some "manual" technologies.
It is incredibly difficult to choose such an angle, therefore, in practice, they try to avoid them, and where they cannot be done without them, they are usually performed in several parts. For example, the jamb in fig. 3, if it were cut, it should have had a joint along the diagonal of the corner. This is the same one usually seen on most wooden door frames.
But in fig. 3 we see that the joint between the parts does not go through the corner, but horizontally. The upper part of the "jamb" rests on two vertical posts like an ordinary beam on supports. At the same time, we see as many as four beautifully executed internal triangular corners! In addition, one of them mates on a complex curved surface! Moreover, all elements are made with very high quality and precision.
Any specialist who works with stone knows that this is almost impossible, especially from a material such as granite. With a lot of time and effort, you may be able to cut one inner triangular corner in your workpiece. But after that, you have no room for error when you cut out the rest. Any discontinuity within the material or inaccurate movement can lead to the fact that the chip will not go where you planned.

Rice. 5 - quality of surface treatment and shape of corners
At the same time, I would like to draw your attention to the fact that these parts are made not just of granite, but of polished granite with a sufficiently high quality of surface treatment.

Rice. 6 - quality of surface treatment and shape of corners.
This quality is unattainable with manual processing. To obtain such smooth and even surfaces, as well as straight edges and corners, the tool must be locked and move along the guides.
But while studying these details, I paid attention not so much to the quality of workmanship and processing, but to how the corners look, especially the inner ones. All of them have a characteristic rounding radius, which is clearly seen in Fig. 5 and fig. 6. If these elements were cut, the corners would have a different shape. And a similar shape of the inner corners is obtained if the part is cast, not cut!
The casting technology well explains all the other design features of this element, and the accuracy of fitting the parts to each other, and the existing arrangement of the joints of the parts, which, from the point of view of design, are more preferable than diagonal seams or a complex part composed of many elements, which inevitably should have been obtained when cutting.
I began to look for other evidence that the construction of this building used the technology of casting from "granite" (in the sense of a material similar to granite). It turned out that in this building, this technology was used in many structural elements. In particular, the foundation of the building, as well as the porch at the two entrances that I examined, were completely cast from "granite", but without "polishing".

Rice. 7 - cast foundation of the General Staff building.

Rice. 8 - another entrance with a cast "jamb" and a porch.
When examining the foundation, attention is drawn to the quality of the "fit" of the sides of the foundation to each other, as well as the rather large size of the "blocks". It is almost impossible to cut them separately in the quarry, deliver them to the construction site and fit them together so precisely. There are virtually no gaps between the blocks. That is, they are visible, but upon closer examination it is clearly visible that the seam is readable only from the outside, and there are no voids inside between them - everything is filled with material.
But the main thing that indicates the use of molding technology is how the porch is made!

Rice. 9 - stone porch, steps are made as a whole with the rest of the elements - there are no seams!
Once again, we see the inner triangular corners, since the steps of the porch are made as one piece with the rest of the elements - there are no connecting seams! If such a time-consuming construction can be somehow explained in terms of "jambs", since this is a "ceremonial detail", then carving a porch from a single piece of stone as a single piece did not make any sense at all. At the same time, interestingly, there is a seam on the other side of the porch, which, apparently, is explained by some technological features of the manufacture of the part, which was not made integral.

We observe a similar picture at the second entrance, only there the porch has a semicircular shape and was originally cast as one single piece, which later gave a crack in the middle.


Rice. 11, 12 - the second semicircular porch. The steps are also integral with the sidewalls.

Rice. 13 - the other side of the semicircular porch, there are no seams at the steps. They are molded as a single piece with the sidewalls of the porch.
Later, walking around St. Petersburg, mainly in the area of Nevsky Prospekt, I found out that the technology of stone casting was used during construction in many objects. That is, it was quite massive, and therefore cheap. At the same time, the foundations of many houses, pedestals of monuments, many elements of stone embankments and bridges were cast using this technology.
It also turned out that the elements of buildings and structures were cast not only from a material similar to granite. As a result, I made the following working classification of the discovered materials.
1. Material "type one", similar to granite, from which the foundations and porches of the General Staff building, elements of embankments, foundations of many other houses are made, including this material was used in the manufacture of foundations, parapets and steps around St. Isaac's Cathedral. By the way, Isaac's steps have the same characteristic features as those of the porches of the General Staff building - they are made as a single piece with a mass of internal triangular corners.


Rice. 14, 15 - parapets and porches around St. Isaac's Cathedral, the steps are made as a single whole with the rest of the elements - there are no seams.
2. Smooth polished granite "type two", from which the "jambs" are made at the entrances of the General Staff building, as well as the columns and St. Isaac's Cathedral. I assume that the columns were originally cast, and only then processed. At the same time, I would like to draw your attention not so much to the inserts, which are much talked about in the films of Alexei Kungurov, as to the way they are glued into the columns. In many cases, it is clearly seen that the material of the "mastic", which was used as "glue", is almost identical to the material of the column itself, but only does not have the final treatment of the outer surface, since it is located inside the seam. Otherwise, this is the same brick-colored filler, inside which black, harder granules are clearly visible. Where the surface of the columns is polished, these granules form a characteristic mottled pattern.


Rice. 16, 17 - the mastic with which the "patches" are glued is actually the same material from which the columns themselves are made.
3. Even smoother "granite", "type three", from which the Atlantean figures are cast. At the same time, the assumption of Alexei Kungurov that they are absolutely identical was not confirmed. I deliberately took a series of photographs from which it can be seen that all the statues have a unique pattern of small details (pile on the bandages), which have a slightly different shape and depth.



Apparently, the technology that was used allowed only one figure to be cast, one original at a time, so for each casting its own original was made. Apparently the original was made from a material such as wax, which melted out of the mold after it hardened.
At the same time, I have not the slightest doubt that these are cast. Not cut-out figures. This is clearly seen on the small elements of the toes, as well as on the characteristic mating radii at the base. These elements are almost impossible to cut from such a brittle material as granite, but they can be easily molded into shape.

But there are other objects in the construction of which this technology was used. This is the building on Nevsky, where the Biblio-Globus store is now located (28 Nevsky Prospect). It is made up of polished blocks that are cast using exactly the same technology. These blocks have a very complex shape that cannot be cut either by hand or with the help of modern mechanisms. At the same time, upon closer examination, it is very clearly seen that the internal corners have rounding radii that are characteristic of castings.




Polished granite blocks of the most complex shape, of which the building at 28 Nevsky Prospekt is composed. It is clearly seen that the blocks are cast as a whole and have many internal triangular corners, including those with a curved surface.
It is possible that there are other facilities built using this technology.
For this material, it should be noted that it has a smoother and better surface than the material "type two" of Isaac's columns or "jambs" of the General Staff building. Apparently this is due to the fact that a more homogeneous and stronger crushed filler was used. That is, it is a later improved casting technology.
4. A type four material that looks like marble. If you go from Iskaia towards the palace square, there will be a hotel, in front of the entrance to which there are two mirrored "marble" lions. They, firstly, have a technological element that is needed for casting, but is completely unnecessary if it were carved by a sculptor - a sprue in the center. In addition, the right lion (if you stand facing the entrance) has a seam on the tail, which clearly shows that it was covered with liquid material, which then froze. Well, again, characteristic radii in all corners, which a sculpture carved with a chisel will not have. When cleaving, the cutter will leave edges, planes, and not correct radii.


As I understand it, most of the "marble" sculptures, including those in the summer garden, were made using this technology, only they did not need sprues, like these lions.
5. Material "type five", which is similar to limestone, in particular to the so-called "Pudost stone", which was used in the construction of the Kazan Cathedral. I do not undertake to assert that in the Kazan Cathedral there are no elements at all that were carved from Pudost stone, it is quite plastic and relatively easy to process, like all limestones. But the fact that during the construction of the cathedral in many places it was casting, where raw materials from this stone were used as a filler, is obvious. The porticoes that close the colonnades have walls between the columns, which are fitted with the greatest precision. Cutting and adjusting them with such precision by hand, especially taking into account the size, and therefore the weight of the blocks, is impossible. But when using the casting technology, this does not pose any problem. In addition, on the very building of the cathedral, it can be seen that some elements are technologically advanced for casting, but completely not technologically advanced and very time consuming for cutting. And in some places, I even managed to find places during inspection where material streaks or traces of covering up the seams or defects in the original casting are visible.





Gathering information for the article, I went to the official website of the Kazan Cathedral, where on the page with the history of construction, among the many illustrations, I found the following figure.

If you look closely, then in this figure we see a form for casting a column, which is assembled from boards and tied with ropes. That is, from this figure it follows that the columns during the construction of the Kazan Cathedral were immediately cast in an upright position!
Moreover, this technology was used not only for the construction of the Kazan Cathedral. I managed to find at least one more building on Nevsky, where the same construction technology was used, at 21 Nevsky Prospect, where the Zara store is now located. But if during the construction of the Kazan Cathedral they simply used material from a quarry, the color of which is heterogeneous, then in this building it was additionally tinted with some kind of dark dye.



In the course of my small research, I discovered another interesting object that finally convinced me that in St. Petersburg, casting technologies were used from materials similar to stone, in particular granite. My hotel was located next to Lomonosov Street, along which it was very convenient to go out onto Nevsky Prospekt to the buildings where our working sessions were held. Lomonosov Street crosses the Fontanka River across the Lomonosov Bridge, the construction of which also used the technology of casting from granite, "type one" material. At the same time, this bridge was originally a drawbridge and it once had a lifting mechanism, which was later removed. But traces from the installation of this mechanism remain to this day. And these traces clearly indicate that the metal elements that once held the structure were once installed in the same way as we now fix metal elements in modern reinforced concrete products. These were the so-called "embedded elements" that are installed in the mold in the right places before pouring the solution into it. When the solution hardens, the metal element is securely fixed inside the part.
The above photographs clearly show the traces of the embedded elements that were once installed in the bridge supports and held the lifting mechanism. Granite is a rather fragile material, therefore, it is practically impossible to gouge holes in it of a similar "triangular" rather than round shape, and even with such sharp edges. But, most importantly, from a technological point of view, hammering all these complex holes simply does not make sense. If this structure was built using traditional technology, then other simpler and cheaper ways of attaching parts to a stone would be used.





In addition, a similar casting or molding technology is used in many buildings as a facade decoration. At the same time, I specifically checked that this is not gypsum, but a hard material similar to granite.




It is interesting that these materials, especially "granites" in their characteristics, apparently surpass modern concrete. They are more durable, have better dynamic characteristics, and most likely do not require reinforcement. Although the latter is just a guess. It is possible that reinforcement is used somewhere there, but this can only be revealed during special studies. On the other hand, if the presence of reinforcement is identified, then this will be a strong argument in favor of casting technology.
Based on the timing of the construction of buildings, at the moment I came to the conclusion that these technologies were used at least until the middle of the 19th century. Perhaps longer, I just did not find objects that would have been built at the end of the 19th century using these technologies. I am still leaning towards the option that these technologies were completely lost during the 1917 revolution and the subsequent civil war.
Some arguments against cutting technology. Firstly, we have just a huge number of stone products. If all this was cut, then how? What tool? For cutting granite, hard grades of specially alloyed tool steels are required. You won't do much with a cast iron or bronze tool. In addition, there will be a lot of such a tool. And this means that there should be a whole powerful industry for the production of such tools, which should have produced tens, if not hundreds of thousands of different cutters, chisels, punches, etc.
Another argument is that even with the use of modern machines and mechanisms, we are not able to separate a whole piece from the rock, from which it will then be possible to make the same Alexandrian column or the columns of Isaac. It only seems that the rocks are a solid monolith. In fact, they are full of cracks and various defects. In other words, there is no guarantee that if the rock seems solid to us on the outside, then it has no cracks on the inside. Accordingly, when trying to cut a large workpiece out of the rock, it can split due to internal cracks or defects, and the probability of this is the higher, the larger the workpiece we want to get. Moreover, this destruction can occur not only at the time of separation from the rock, but also at the time of transportation and at the time of processing. Moreover, we cannot cut out a round blank at once. At the beginning, we will have to separate a certain parallelepiped from the rock, that is, make flat cuts, and only then split off the corners. That is, this process is simply very, very time consuming and complicated, even for today's time, not to mention the 18th and 19th centuries, when, supposedly, all this was done by hand.
At the same time, during my little research, I came to the conclusion that the use of granite columns as the basis for the supporting structure of buildings in the 18th and 19th centuries in St. Petersburg was a fairly common technical solution. Only in two buildings in Rossi (one of which is now a ballet school), a total of about 400 columns are used !!! On the facade, I counted 50 columns, plus the same row on the other side of the building, and two more rows of columns are inside the building itself. That is, we have 200 columns in each building. An approximate calculation of the total number of columns in buildings in the area of Nevsky Prospekt and the city center, including temples, cathedrals and the Winter Palace, gives the total number of about 5 thousand granite columns.
In other words, we are not dealing with separate unique objects, where, with some stretch, one could assume that they were made by forced slave labor. We are dealing with an industrial scale of production, with mass construction technology. Add to this also hundreds of kilometers of stone embankments, and also with a very figured and high-quality finish, and it becomes obvious that no slave forced labor can provide such a volume and quality of work with cutting technology.
To build and process all this, firstly, casting technologies had to be massively used. Secondly, for the final finishing, mechanized surface treatment is used, in particular, the same Isaac's columns or "jambs" of the General Staff building. At the same time, a lot of raw materials were needed for the casting technology. That is, the stone, obviously, was mined in quarries near the city, but after that it had to be crushed, which means that there had to be stone crushers with high productivity. You cannot crush so much stone to the desired consistency manually. At the same time, I assume that it is most likely that the energy of water was used for these purposes, that is, it is necessary to look for traces of water stone mills, of which, judging by the scale of the use of technology, there should have been a lot in the vicinity. This means that references to them should also be in historical documents.
Dmitry Mylnikov, Chelyabinsk
November 2013 - April 2014
Recommended:
Historians are FORBIDDEN to go there. Baalbek construction technologies that we CANNOT repeat

If you have ever been interested in amazing structures, looked on YouTube about the Egyptian pyramids, megalithic complexes like the English Stonehenge and the Armenian Karahunj, then you must have heard about Baalbek
Technologies of Civilization Lost in the 17th century

In the Middle of the 17th Century, a Global Catastrophe took place that affected all continents of the Earth and led to the death of Civilization, all this can be understood, including through the study of the technical level of a lost civilization. So many technologies that we see in the middle of the 17th century are not mastered today
Lost Technologies: Arc de Triomphe

Finally, another "wonder of the world" opened in Moscow. Thanks to the restoration of the Arc de Triomphe and the talkativeness of journalists, details of the industrial power of Russia at the beginning of the 19th century, carefully hidden for many years, became known
TOP 4 scientific technologies lost in the USA

Many creators associate the United States with the advanced country of high-tech, information technology, Hollywood, Silicon Valley and many others. Of course, this is partly the case. But as they say, there are spots on the sun. and for the United States … Today I will tell you about four technologies that the United States has lost. And maybe forever
Why was the monorail superseded from the construction technologies of the 20th century?

With the onset of the scientific and technological revolution, transport began to develop by leaps and bounds. Therefore, it does not seem surprising that almost immediately after the appearance of the railway in its traditional form, a monorail began to be built in a number of countries. And it spread rapidly around the world. A hundred years ago, it was considered almost the most promising type of transport, which in the future will be at every step