Table of contents:
- Tenacity of the breed
- Gold and ice
- Gifts from the bowels
- Tons and grams
- Underground on a Toyota
- Foam stone
- Molecule Adventures

Video: How gold is pumped out of the planet
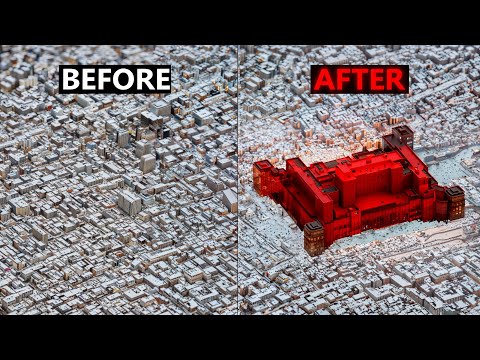
2024 Author: Seth Attwood | [email protected]. Last modified: 2023-12-16 15:55
The prospector scoops up one or two shovels of soil from the bank or from the bottom of the river, throws it into a tray with a concave bottom, and then for a long time washes away clay, sand and pebbles in the water, peering intently into the muddy suspension - won't something shine? The reward is a few yellow grains of sand at the very bottom of the tray. Or a small nugget, if you're lucky …
Well, now we will tell another story about gold mining. A story that has almost nothing to do with the above.

Strictly speaking, pure gold exists purely in theory. Even in 999.9 gold, from which bank bars are made, there is, as can be understood from the index, one ten-thousandth of impurities. But such gold is an industrial product. There is no need to think about finding something similar in nature.
Gold sand washed by prospectors or mechanized dredges is actually just a raw material, a concentrate, which will melt more than once and undergo dissolution-precipitation (refining) before being cleared of many impurities. And yet, it is easier to work with placer gold than with gold from primary deposits, where the yellow metal remains embedded in the rock - rarely in the form of veins and often in the form of microscopic particles invisible to the naked eye, in fact, finely dispersed dust.
In the latter case, trays, dredges, and any other tools are useless - you need to call on chemistry for help.

Tenacity of the breed
The classical method is the processing of crushed ore with an aqueous solution of sodium cyanide in the presence of oxygen (cyanidation). Gold is actually washed out of the ore: its atom combines in solution into one ion with carbon and nitrogen. Then gold is precipitated from the solution (together with a number of impurities, primarily with silver).
But the most difficult case is the so-called refractory ores. In them, gold dust grains several microns in diameter are enclosed in sulfide shells consisting of pyrite (compounds of sulfur and iron) or arsenopyrite (iron, sulfur, arsenic). The problem is that sulfide shells are not wetted or dissolved by water, so direct cyanidation of refractory ore will give almost nothing.
It is necessary to somehow break this shell and remove the precious speck of dust from it … Or maybe you don’t need to suffer - why are the good old trays and dredges bad? Necessary! All over the world, placer deposits are close to depletion, and the bulk of the world's gold is already produced from ores, including refractory ores.
Gold and ice
It is ores of this type that are mined at the site of the Albazino Resources Mining and Processing Plant (GOK), owned by the Russian company Polymetal - the second in Russia in terms of gold mining. Here is the edge of the hills covered with thin taiga, an almost uninhabited corner of the huge Khabarovsk Territory.
There are more than a hundred kilometers from the ore production, where 1, 2 thousand employees work exclusively on a rotational basis, to the nearest settlement. The city of Amursk, where the products of the GOK are processed at the local hydrometallurgical plant, is about four hundred kilometers.

The road from Amursk to Albazino is about two-thirds unpaved and the same two-thirds goes through the dense taiga. Hundreds of kilometers without settlements, gas stations, roadside cafes and cellular communications.
Here the driver's companion is a walkie-talkie. Traffic participants listen to the same frequency in order, if necessary, to convey to the “neighbors” some information concerning the situation on the road, to warn about something, to ask for help. You can only get through to the outside world from a satellite phone, but this is not an affordable luxury for everyone.
Approximately 50 km away, the road to Albazino is blocked by the fast and full-flowing Amgun River, the last large tributary of the Amur before it flows into the Pacific Ocean. In the summer there is a ferry, and in the winter there is an ice crossing. The crossing is specially strengthened by pouring water on it and freezing an additional layer of ice, so that the river in winter is calmly crossed not only by cars, but also by tractors loaded with 42 tons of flotation concentrate (with GOK products) with trailers.
Gifts from the bowels
Local hills are not high, but they are participants in the process of a planetary scale. America and Eurasia are gradually colliding with each other, creating a huge seismic stress along the entire perimeter of the Pacific Ocean.
This perimeter is called the Pacific Ring of Fire. Land folding in the Russian Far East also resulted from the collision of continental and oceanic plates. And of course, volcanoes erupted in these parts. Together with liquid magma, they carried gold from the depths to the surface, creating future deposits.
Traces of an ancient volcanic caldera (a volcano that collapsed inward) were also found in the Albazino mine area.

In the depths of the antisynclinorium, under the layer of "young" Quaternary deposits (clays, loams), there are sedimentary rocks such as sandstones - they arose as a result of the weathering of more ancient mountains. Here and there, sedimentary rocks are cut from the bottom up by narrow dikes - wedges squeezed out of the bowels of magma. It is in these dikes that geologists find gold bodies.

Tons and grams
Not so long ago, we published a report from a copper mine and said that the copper ore mined by the mine method contains only 3% copper. It seemed that this is very little - only 30 kg of valuable metal per ton of mined stone! The ore, which is mined in Albazino Resources, contains on average 0, 0005% of gold, in other words - 5 g per ton.
Is it really cost effective? At the current world price of gold (about $ 1,600 per troy ounce - 31.1 g), it is quite. But it sounds impressive: there is as much precious metal in a standard bank gold bar (about 12 kg) as in 27 full-ore mining dump trucks with a carrying capacity of 90 tons each. In reality, more trucks will be needed to get the ingot: there are no industrial methods for one hundred percent extraction of gold from ore yet.
The 90-tonne dump trucks are used in quarries - where gold is mined in an open pit. There are several careers here, and all of them are named by female names.
The most productive one for today is Anfisa, the Olga quarry has already been worked out and closed. The life of a quarry begins with geological exploration, which is carried out by the methods of core drilling, when a cylindrical sample is drilled out of the rock, and cuttings, when crushed rock extracted from the well is analyzed (this is an easier and cheaper method). The geologists' data are sent to the mining planning department, where, with the help of software, a model of the ore body occurrence is built and the most economically feasible ore mining scheme is created. Then the work of creating a quarry begins.

The first step is to remove the overburden - the soil covering the ore horizons. Well, then methodically, every day, wells are drilled in one or another section of the rock, which are filled with explosives, and after a small check, excavators and dump trucks come to the blast site to select the ore and take it to the local mining and processing plant.
The quarry develops downward, its gently sloping sides converge towards the center in concentric ledges: between the horizons, "shelves" - berms are left. Some of them are narrow and serve only for the structural strength of the mine, others are used as transport routes for technology. The quarry - majestic like a Roman amphitheater - gives an impression of solidity that can be deceiving. Therefore, the sides of the quarry are constantly scanned by a special radar capable of tracking the slightest movements of rock masses. It's calmer this way.
Quarries go 200–300 m deep, but most often the ore body has a narrow oblong shape and continues even lower. Theoretically, you can create a deeper quarry, but in order to withstand the gentle slope of the sides, you would have to dig a bowl of huge diameter and spend a lot of time and energy to excavate completely excess rock. Exit? Underground mining.

Underground on a Toyota
At the bottom of the Olga open pit, where open pit mining has been completed, there is one of the entrances to the Albazino Resources underground kingdom. Into the depths of the serpentine road we are driven by the "unkillable" Toyota Land Cruiser 70, specially modified by one of the Canadian firms for travel through mine workings. Below is the usual mine life: drilling rigs drill holes for laying explosives, stocky squat bucket machines take out the crushed ore, and then transfer it to special mine dump trucks.
If we imagine an ore body as a kind of column going into the depths, then its development is carried out as follows. First, inclined ramps (those same serpentines) break through from the bottom of the open pit on the sides of the ore body (in the waste rock). Then between the exits (also bypassing the ore), transport drifts, or simply tunnels, are made. And now from them to the ore rush-orts rush.
Machinery enters them and turns a whole segment of the "column" into crushed stone, which is taken out to the mountain. But leaving the huge mined-out cavity is dangerous, so before the miners go down to mine the next horizon, the voids left from the selected ore are poured with concrete. In South Africa, there is the Mponeng gold mine, which goes down four kilometers.
In Albazino, the order of depths is more modest: hundreds of meters, but the total length of the underground penetration is impressive. Since 2009, miners have passed over 100 km of tunnels.

Foam stone
Whether taken from a quarry or mined in a mine, the ore ends up in piles (heaps) next to the ore processing plant. Ore can be black, gray, almost white, brownish, but no signs of gold are visually detected on it and it is impossible to distinguish it from waste rock by sight. However, color isn't the only difference.
With an average of about 5 g of gold per ton, ores with a grade of 2 g or less to 3 kg per ton are found here. Raw materials also differ in strength and extractability. To use ores of different quality in the work, but to produce products (flotation concentrate) within the framework of planned indicators, different ores are charged, that is, they are mixed in a certain proportion.
The essence of what is happening at the GOK can be summed up in two words: grinding and flotation. In order to cut off the maximum excess and take away from the raw materials as many tiny gold-containing particles as possible, the ore, or rather the slurry - water suspension, is ground in huge drums in the presence of balls of high-strength steel. The grinding product is sent for cycloning (vortex separation) of coarse and fine fractions.
The finest dust goes to flotation, coarse grains to regrind. Sulfide films surrounding gold, as already mentioned, are not wetted with water. This is a problem for the chemical recovery of gold, but for beneficiation, which is based largely on physical processes, the disadvantage becomes an advantage. The pulp is saturated with air, foaming compounds of high molecular weight alcohols are added to it.
The bubbles surround the sulfide "capsules" and lift them upward. Valuable foam is discharged, and the ore, which is still in the flotation machine, goes for regrinding and again for flotation. The result of the entire multi-stage process is a solid sludge (cake) squeezed out of the foam, called flotation concentrate. The last stage is drying in a drum, where the cake is brought to a standard moisture content of 6%. The dry concentrate is loaded into special bags containing 14 tons of raw materials. Three of these bags are put on a platform with a tractor and go to Amursk, to the metallurgists.

A few numbers. From the ore supplied to the GOK, an average of 85–87.5% of gold is recovered. The flotation concentrate no longer contains 5, but 50 g of valuable metal per ton. Thus, a standard bank ingot contains approximately the same amount of gold as raw materials transported on 6 trailers with a load of 42 tons each. Impressive!
Molecule Adventures
Only the Amur Hydrometallurgical Combine gives us an answer to the question of how, after all, to remove the gold from the persistent shell. Here, at an enterprise also owned by Polymetal, the so-called autoclave technology was used for the first time in Russian gold mining. The autoclave is actually a furnace: a long, horizontal steel cylinder, internally covered with an acid-resistant membrane and lining - three layers of heat-resistant and acid-resistant bricks.
Pulp (a mixture of flotation concentrate with hot water) and pure oxygen are fed into the autoclave under pressure, and the exothermic reaction of sulfur oxidation is triggered. Pyrites and arsenopyrites disintegrate, and free gold appears in the mixture. In the photo below is the most spectacular moment: the brown cathode precipitate is melted into a light yellow Doré alloy. The hot metal is poured into ceramic molds (molds).

But that's not all: there is a real chemical thriller ahead. After the evaporator (where the temperature and pressure of the slurry drop sharply), the mixture is sent for neutralization - removal of the sulfuric acid formed during the reaction. Cyanidation is ahead (which will finally become possible), and sulfuric acid, when dissociated in solution, forms a positive hydrogen ion.
When met with cyanide, hydrogen readily combines with cyanide ion (CN) to form hydrocyanic acid (HCN), which will evaporate. Therefore, sulfuric acid must be removed by neutralization, and only then, during cyanidation, gold can form an ion - dicyanoaurate. Charged, these ions stick to the activated carbon specially added to the pulp. All this is called sorption, but at the desorption stage, the NaOH alkali solution literally flushes gold-containing ions from the coal, which are sent to the electrolyzer.
There dicyanoaurate decomposes and finally pure gold is deposited on the cathode. The brown sediment is sent for smelting and there it turns into light yellow nostril heavy ingots, shaped like bank ones. But this is still not gold, but the so-called Dore alloy, where there is about 90% gold, a few percent silver, and also nickel and copper. These metals love each other so much and dissolve in each other so easily that it is possible to isolate 999-carat gold only during refining. But another company will be engaged in refining. The gold miners and metallurgists of Polymetal have done the main work.
Recommended:
Underground city Ramenki-43 near Moscow turned out to be fiction

The undergrounds of Moscow have been exciting the minds of researchers for decades. Some of them are conditionally accessible and, if desired, you can go there for an excursion accompanied by diggers, others are closed and securely guarded. But there are also places where not only there is no way for mere mortals, but also whose very existence can be determined only by indirect signs, for example, the underground city of Ramenskoye-43, covered with legends no worse than the lost library of Ivan the Terrible
What reforms in Russia did Peter I carry out?

Peter I, the tsar-reformer, the tsar-revolutionary, under whom Russia received the status of an empire, from the first days of his reign was not like his predecessors
How soon will the planet run out of oil?

Compared to the topic of global warming or even a very hypothetical threat of a collision of the Earth with the asteroid Apophis, the peak of oil production
GOLD TO LONDON! (c) the Central Bank of the Russian Federation. Russian gold flowed to the West, which was not even during the War

Using gold to plug currency "holes" in the Russian economy is sheer barbarism. Gold should not be exported, but accumulated. Especially considering the continuously rising prices for the precious metal. First of all, it is necessary to increase gold reserves as part of the international reserves of the Russian Federation
Kolchak's GOLD CAN BE RETURNED! Japan grabbed the gold reserve of the Russian Empire, and now wants the Kuril Islands

Recently, Maria Zakharova said that Russia could raise the issue of tons of tsarist gold remaining in Japan